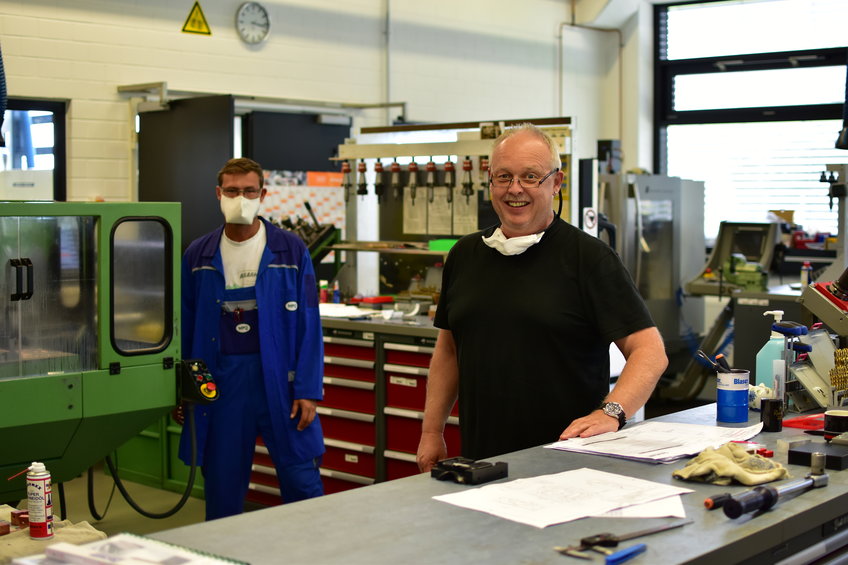
No Place for Know-It-Alls
Michael Rogg is head of the MPQ mechanical workshop that produces components that are indispensable for research.
Due to the COVID-19 pandemic, Michael Rogg currently works from home. He plans the schedule and does some computer programming. His department decided to split the team into two groups that work with alternating weeks. In the case of an infection, not the whole department will have to go into quarantine but at least half the team can continue working. This is important since not all the work can be done digitally: “We have less work at the moment because fewer researchers are allowed to work in the labs, but there are still a number of components we have to produce.”
Michael Rogg is head of the mechanical workshop at the MPQ and therefore part of what researchers praise as “an outstanding research environment.” Whoever at the MPQ needs a component for their experiment can place an order with the mechanical workshop and will receive the requested item within two weeks at the latest. Many of the produced components are unique and quite often the mechanics have to experiment themselves. “Sometimes, researchers ask for items that no one has ever manufactured. In those cases, we simply have to experiment and see whether it works.”
Michael Rogg knows the institute like almost no one else. Since 1986, he has been working at the MPQ, and since 2012, he has been head of the mechanical workshop. Even his training he received at the nearby Max-Planck-Institute for Plasma Physics. Precision mechanics has undergone great changes in the last decades. Originally a job that demanded a lot of craftsmanship, the precision mechanic of today needs to be able to work with CNC-machines as well as program computers. “Some of the milling machines are computer based, which is why the complexity of the components has increased considerably,” says Michael Rogg.
His department has 17 employees, four of which are apprentices. The dual training model only exists in Germany: over the course of three and a half years, apprentices learn a specific profession and divide their time equally between practical on-the-job-training and theoretical course work at school. There are over 300 qualified apprenticeship jobs in Germany. At the MPQ mechanical workshop, there are three trainee precision mechanics and one trainee construction mechanic; furthermore, there is one apprentice position in the administration.

Since some of the machines are now computerized, both employees and trainees are required to continually extend their knowledge and learn how to program; to Michael Rogg’s dismay, programming still isn’t included in the official training regulations: “It is absolutely essential, if you don’t know how to program, you can’t do our job properly.” At the MPQ, trainees become all-rounders of their subject. For Michael Rogg, that is a matter of honour, but also a necessity. “In industry, trainees often only work with one or two machines, in our workshop they need to learn it all.”

58-year old Michael Rogg taught himself how to program, by attending workshops and reading books. For him, lifelong learning is a natural part of his job: “If you like your job, you enjoy learning new things.” When he is at home in the evening, he usually keeps himself busy reading. He is fascinated with old drawings of mechanical components and machines. “It’s just amazing, you can tell from these drawings that people 80 or a 100 years ago worked just as accurately as they do today.”
Around Christmas, all current and former employees of the department meet. Only few trainees have ever dropped their apprenticeship, but some of them quit after finishing to study at university. Among some of his previous trainees are several engineers who received their diploma by attending evening school, and then went on to study at university. Surprisingly, none of the trainees at the mechanical workshop at the MPQ holds a secondary school diploma. Even students who only hold a middle school diploma - commonly said to be in low demand on the labor market - can get a chance at the MPQ. “We need people who really want to learn the job, no know-it-alls”, says Rogg.

The trainees learn to work with the two types of machines commonly used in precision mechanics - the milling machines that produce angular-shaped components, and the lathe that produces circular components. With both machines, the precision mechanics can work as accurately as the hundredth of a millimeter. By way of comparison: the diameter of a human hair is circa five-hundredths of a millimeter. Crucial for the result is the choice of tool. Different tools can be used for each machine; which tool you use depends on the material: “The general rule is: the harder and denser the material, the blunter the cutting angle needs to be,” Rogg explains. “In other words: you can cut a piece of cheese with a razor blade, but not a piece of metal.” The materials used at the MPQ often cause him headaches. “Some materials are used only in research and astronautics; there simply are no specific tools. In those cases you have to rely on your own experiences and figure out which material has similar attributes and find alternatives.” Generally, the precision mechanics work according to wishes of the researches, but sometimes it’s worth asking for more detailed information. “If the requested measures are in the range of thousandths of millimeters, I will ask whether that’s really necessary for the experiment. In other cases, I’ll ask whether it has to be that really expensive material. Often it turns out that the requirements are that specific because that’s what they read in an academic journal or heard at a conference, but there are easier and cheaper ways.”

It is a bit painful for him if components that he or his employees spent a lot of time working on end up in the trash within a shorly after. “That hurts, but it is part of the process. We’re doing top-level research here, so sometimes you just have to dismiss certain ideas.”
In his free time, he enjoys driving his motorcycle and acting in Bavarian theatre plays. “Initially, I only helped out because they needed people who knew the Bavarian dialect for a play, but now I often play the main part.” Moreover, his passion for building is in high demand with his three “bonus grandchildren”; he repairs broken toys and is planning larger crafts projects. He calls them “bonus grandchildren” because they are the biological children of his female partner’s daughter. For him, that makes no difference, though: “I’m the first to become a grandfather in my friendship group without being even a father,” he says laughing.
(AE)